Upper and lower bound force capacity estimates of lead extrusion damper design force using classical extrusion models
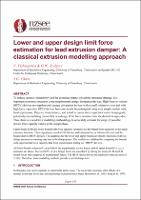
Download
Date
2021-04-14Authors
Vishnupriya, Vishnupriya
Rodgers, Geoffrey
Chase, Geoff
Metadata
Show full item recordAbstract
To reduce seismic vulnerability and the economic impact of seismic structural damage, it is important to protect structures using supplemental energy dissipation devices. High force to volume (HF2V) devices are supplemental energy dissipation devices with a small volumetric size and with high force capacities. HF2V devices have previously been designed using very simple models with limited precision. They are manufactured, and tested to ensure force capacities match design goals, potentially necessitating reassembly or redesign if the force deviates from the desired design value. Thus, there is a need for a modelling methodology to accurately estimate the range of possible device force capacity values in the design phase.
Upper bound (UB) and lower bound (LB) force capacity estimates are developed from equations in the metal extrusion literature. These equations consider both friction and extrusion forces between the lead and the bulged shaft in HF2V devices. The equations for the lower and upper bounds are strictly functions of device design parameters ensuring easy use in the design phase. The models are validated by comparing the bounds with experimental force capacity data from experimental testing on 15HF2V devices.
All lower bound estimates (FLB) are below the experimental device forces, and all upper bound (FUB, indirect) estimates are above. Precise HF2V device design forces are calculated by taking the mean of LB and UB model forces and compared to experimental forces. The HF2V device forces are predicted within an error of 1-16%. Therefore, these modelling methods provide a useful design tool.